丝印油墨在标签印刷领域的应用体会
2011-02-16 10:06:58.0 来源:标签与贴标 责编:Victoria
- 摘要:
- 丝网印刷起源于我国,与平版印刷、凹版印刷、凸版印刷并称为四大主流印刷技术。由于其印刷方式的独特性以及印刷材料的广泛性,除去一般的纸张印刷外,也被广泛应用于电子工业、陶瓷贴花工业、纺织印染等行业。近年来,丝网印刷工艺更是在模内注塑、广告、招贴标牌等行业中被大量采用。
【CPP114】讯:丝网印刷起源于我国,与平版印刷、凹版印刷、凸版印刷并称为四大主流印刷技术。由于其印刷方式的独特性以及印刷材料的广泛性,除去一般的纸张印刷外,也被广泛应用于电子工业、陶瓷贴花工业、纺织印染等行业。近年来,丝网印刷工艺更是在模内注塑、广告、招贴标牌等行业中被大量采用。
模内标签
模内注塑技术即IMD(In-Mold Decoratiom),IMD是目前国际风行的表面装饰技术,常用在手机视窗镜片及外壳、洗衣机控制面板、冰箱控制面板、空调控制面板、汽车仪表盘、电饭煲控制面板多种领域的面板、标志等外观件上,集装饰性与功能性于一身,其产品已经进入千家万户。
通常的IMD工艺按照最终的产品表面是否有一层透明的保护薄膜,可以分为分为IML(IN-MOLD FILM/LABEL)、IMR(IN-MOLD ROLE)。
IML的中文名称是模内镶件注塑。其工艺非常显著的特点是:表面是一层硬化的透明薄膜(PC或者PET),中间是印刷图案层,背面是注塑的树脂层。油墨夹在薄膜和树脂中间,可使产品防止表面被刮花和耐磨擦,并可长期保持颜色的鲜明不易退色。
IMR的中文名称是模内转印(热转印或者热转写),此工艺是将图案印刷在薄膜上,通过送膜机将膜片与塑模型腔贴合进行注塑,注塑后有图案的油墨层与薄膜分离,油墨层留在塑件上而得到表面有装饰图案的塑件,在最终的产品表面是没有一层透明的保护膜,膜片只是生产过程中的一个载体。但IMR的优势在于生产时的自动化程度高和大批量生产的成本较低。IMR的缺点:印刷图案层在产品的表面上,厚度只有几个微米,产品使用一段时间后很容易会将印刷图案层磨损掉,也易褪色,造成表面很不美观。另外新品开发周期长、开发费用高,图案颜色无法实现小批量灵活变化也是IMR工艺无法克服的弱点。
模内注塑工艺是一项新兴工艺,同时也是一项综合性很强的工艺,它牵扯到油墨、薄膜片材、注塑树脂、注塑模具等。在这几项中任何一项出现问题,都会影响最终的产品,并给厂家造成损失。以下就这几项进行逐一分析,希望给大家提供有用的帮助。
(1)片材
模内注塑目前使用的印刷片材主要是PET、PC材料,以及PMMA。其中使用最多的是PET材料,市场上的PET材料种类繁多,既有正规大厂出产,又有其他来源的。如果最初的印刷材料没有进行一些必要的测试后,就会导致薄膜材料和油墨之间没有附着力,导致后面一系列的工艺徒劳无功。建议模内注塑的客户在使用不同批号的材料做注塑后,首先对材料的进行一些测试:
比如:利用油墨的附着力测试,来测试油墨是否在此材料上有附着。材料的耐温性测试,测试后期注塑时,材料是否可以承受注塑模具中的温度。
其实在进行油墨附着力测试最好的办法就是直接用UV油墨来测试,目前业界一般的UV油墨都必须在经过易附着处理的材料上印刷才会有附着力,如果UV油墨在此材料上有附着力的话,溶剂型油墨在材料上印刷肯定不会有问题。
(2)油墨
目前市场的注塑油墨以日系(十条、帝国、精工)和德系(宝龙)居多,国内有厂家在成产,但是在实际应用中较为少见,也较少有成功的案例。
油墨在使用过程中,一般需要注意如下问题:
a.油墨在薄膜材料上没有附着力
同油墨厂家确认油墨的使用范围使用条件,是否需要添加固化剂,是否需要专用稀释剂;同薄膜厂家确认薄膜的种类,以及是否经过一些易附着处理;
b.油墨印刷过程中会凝固、不下网。
一般的油墨添加固化剂后,油墨的使用时间会有所限制,有的油墨在添加两种固化剂以后,使用时间会变的更短,因此在印刷之前需要向厂家确认清楚;如果是单组份油墨只需添加稀释剂即可。
c.油墨在注塑时,出现“冲花”现象。
原因分析:油墨不耐高温所致或者油墨直接接触到了高温注塑树脂。
模内注塑工艺中,一般都在薄膜印刷的最后印刷一层溶剂型胶水,胶水一般起两方面的作用:黏着作用,使薄膜和注塑的树脂更加好的黏合在一起;保护油墨层,注塑过程中,高温树脂首先会融化已经完全干燥的胶水,在融化胶水的过程中,树脂的热量被部分吸收,进而减少油墨因为高温树脂所致的变色现象。
所以最后一层的胶水印刷,一般推荐低目数印刷(250目左右),一到两遍,保证胶水尽可能的厚。
同时油墨的皮膜干燥时间适当延长,温度适当提高,或者增加固化剂的添加比例,以此来提高油墨皮膜的硬度也会可以保证油墨具有较好耐冲性。
其他原因在模具部分中阐述。
d 注塑产品,树脂部分和薄膜分离
油墨是否完干燥完全,油墨中会有稀释剂、印刷过程中要添加稀释剂,在印刷最后稀释剂如果没有完全挥发就去注塑的话,会在注塑中继续挥发,由于此时树脂和确认黏合剂是否和注塑的树脂相配套。
电子标签印刷
所谓电子标签,就是指印刷后用在电子产品上的标签。如笔记本上的“windows”标示标签、生产厂家标签以及笔记本电池上面的标签。
电子标签使用的材料一般以PET、PC材料和合成纸为主,以及在PET材料上作出各种效果拉丝效果,磨砂效果等等。应用在电子标签上的油墨国内国外的厂商都有,价格和质量也是相差很多。
电子标签印刷的油墨在使用的过程中主要存在以下问题:
a.油墨在印刷材料上附着不好。解决方式:确认油墨和材料是否匹配;确认油墨是否干燥,一般的丝印油墨因为印刷的墨膜比较厚,所以需要采取强制干燥的方式来加快油墨的附着。如果是自然干燥,时间要保证充分;添加必要的固化剂。
b.印刷后的墨膜出现墨斑等现象。
解决方式:确认使用的稀释剂是否和油墨相配套,稀释剂是否可以充分溶解油墨;确认油墨在使用时是否充分搅拌,一般来说油墨在新开罐时,其树脂颜料会沉淀在罐子的底部,这时需要充分搅拌一段时间去除墨样,加入稀释剂,加入稀释剂后仍需进行充分搅拌,保证油墨里面的树脂、颜料与稀释剂充分混合。印刷过程中,由于稀释剂的挥发,必要时在网版上酌情添加稀释剂,并搅拌;重叠印刷时,确认保证首印刷面的整洁,不要落下灰尘,避免水渍、汗渍;添加固化剂的油墨要保证固化剂和油墨、稀释剂均匀混合;确认胶刮的刀口部分是否有缺陷,是否需要更换新的胶刮。
c.油墨的黏度值较大,无法印刷。
解决方式:添加必要的稀释剂,UV油墨需要专门配套的稀释剂;油墨充分搅拌或者边加热边搅拌,特别适用于UV油墨,冬天温度低,油墨的黏度值大,如果依靠添加稀释剂会影响UV油墨的固化。
d.油墨的黏度值较小,像水一样在流淌,无法印刷。
解决方式是:建议添加适量的粉类物质,如消光粉(光泽型油墨不推荐),添加量一般在3%以内;同样可以把油墨放置在温度较低的环境(如冰箱)一段时间。
e.油墨出现气泡的原因及解决方法
出现气泡的原因有下面两种情况:含硅的油墨与非含硅油墨在一起使用时出现气泡;温度的变化导致油墨黏度的变化也会出现气泡,黏度大气泡容易出现。
解决方法:同油墨厂家确认使用的油墨的类型,比如调色时同是印刷在PET上的两系列的油墨,是否可以混用。在同一系列的油墨调色时,确认清漆和有色墨是否可以混用;添加消泡剂,并同油墨厂家确认此消泡剂的适用范围(适用于含硅油墨还是不含硅油墨);添加稀释剂,油墨充分搅拌后,要稍微静置一段时间。
f.印刷的皮膜表面出现针孔
针孔的外观首先是气泡,在干燥的过程中气泡破裂,周围的油墨没有及时流平,便已经干燥,这时出现针孔。印刷车间不洁净,存在灰尘、印刷材料表面有油污等原因都会造成针孔现象的出现。一般来讲,针孔现象是不可避免的,某些数目的针孔也是在可允许范围之内的。但是采取以下措施可减少针孔的出现:
重复印刷,印刷两遍以上;降低印刷目数,比如300目减为250目;使用无尘车间,减少灰尘;使用慢干性稀释剂,减慢稀释剂的挥发速率;增加胶刮的压力,放慢印刷速度。
g.印刷细小的文字、网点图像时,文字和网点丢失。
在印刷过程中,由于油墨干燥太快,导致细小文字和网点无法顺利的从网版转印到承印物上。
解决方式:使用UV油墨来印刷。UV油墨由于不含有挥发性溶剂,在细小文字和网点印刷时有较好的再现;换用慢干型的油墨或者油墨中添加慢干稀释剂,延缓油墨的干燥。
日化标签印刷
日化用品主要是PP、PE材料。这一类材料由于表面张力值较低,需要采取一些措施增加其表面的的张力值,来增加油墨的附着力。常用的增加表面张力的方法有:化学处理,火焰处理,电晕处理等。
值得注意的是,经过火焰处理后的塑料表面的效果有时效性,会在一定的时间之后消失,需要及时印刷,笔者所见过的最有成效的印刷方式就是火焰处理和印刷联动操作,火焰处理一般使用的是天然气。
有些客户在使用UV油墨印刷PP、PE材料时,经常出现印刷后的图案或者文字经过UV固化后缩小的现象。原因主要是UV油墨的黏度值太低,可以改用高粘度的UV油墨。
化妆品包装经常使用一些玻璃的标签材料,在此类材料上印刷时一般以强制干燥的油墨为主。干燥的温度和时间一般在100~130℃,30~50min为宜。
由于此类油墨一般为双组份油墨,在使用此类油墨时一定要注意选择合适的油墨稀释剂,确保稀释剂、油墨、固化剂三者之间良好的互溶。
特殊类的油墨的印刷
1.印刷线路板时使用的导电碳浆、绝缘油墨、导电银浆。
首先这一类使用的印刷材料一般是未经处理的PET材料,使用的导电碳浆一般以溶剂型为主,绝缘油墨常以UV型为主,银浆以溶剂型为主。
使用此类油墨时,需要注意如下问题:
a.先期的测试实验是必不可少的,测试油墨的附着力,测试油墨电阻值、耐电压、电阻率等等。
b.同时印刷时最好要在无尘环境中操作,防止灰尘落在本来就非常细小的印刷线上。
2在丝网印刷中,目前使用的银墨中镜面银较多。关于此类油墨的印刷需要注意以下事项:
a.银墨印刷时,因为其中银粉的粒径不同,需要采用不同的网目来印刷。对于粒径较大的网目一般在200目左右,才能保证银墨中银粉能够通畅的被印刷在承印物上。否则如果使用较高网目的话,在印刷初始是可以的,但随着印刷的进行,银粉中粒径较小的颗粒被转移到承印物上,较大的颗粒则留在网版,容易造成网目的被堵,无法继续印刷。
b.镜面油墨由于本身黏度值较小,像“水”一样。在印刷时,必须快速印刷,防止油墨在网版的流淌、渗透污染到承印物,同时镜面油墨的干燥最好在冷风下干燥,这样获得的镜面效果最好。
镜面油墨里面的金属成分较多,印刷时一般不耐折,不耐划伤,印刷时需要注意尽量不要把镜面油墨印刷在模切的位置,避开模切工具的冲击。印刷完镜面油墨后,在其背面要有打底的油墨来保护镜面层,并需确认镜面油墨和起保护作用的油墨是否会反映影响镜面油墨的镜面效果。
丝印油墨的调色
在丝网印刷工艺中,需要调制的油墨也较多。由于丝印油墨调制墨没有同一的标准可参照,不同的油墨厂家里面的颜料体系不一样,实际生产不同的工艺都会影响丝网油墨调的颜色。下面就丝网印刷油墨的调色谈一下自己的体会。
1、调色前的准备工作:
首先调色以前需要和客户确认如下事项:印刷材料是何种种类?印刷材料有无底色?印刷材料的哪一面需要印刷?调色墨需要印刷几遍?印刷的网目数?印刷完调色墨以后是否需要打底色,印刷打底色需要的网目数?
2、丝网印刷调色的工作有时不是一次调色就能让客户满意的,如果客户认为调出的颜色有偏差,需要注意以下问题:
首先调色时,客户经常会提供潘通色号作为标准,但是由于潘通色卡只是胶印使用的色卡,且胶印和丝网印刷存在较多的差异,所以调色只能做到颜色接近。其次同一家的油墨还原同一家的调色墨基本没有问题。最后用一家的油墨来还原其他家的油墨,由于油墨配方的问题,也是只能做到大致接近。
同时在调色时,调色师傅通常会将自己调的颜色先行印刷一下测试印刷效果,如果调色师傅的印刷效果客户认可,客户自己印刷时却没有印刷出这种效果的话,一般应从客户打样时的印刷目数高低、印刷压力大小、网版乳胶厚薄、刮刀硬度及印刷速度来综合考虑分析。
【点击查看更多精彩内容】
相关新闻:
涨价狂潮下油墨等原材料的价格将走向何方
油墨使用知识十问十答
2011年印刷产业发展:油墨等原材料价格走向何方
油墨出现粉化现象的原因及解决方法
模内标签
模内注塑技术即IMD(In-Mold Decoratiom),IMD是目前国际风行的表面装饰技术,常用在手机视窗镜片及外壳、洗衣机控制面板、冰箱控制面板、空调控制面板、汽车仪表盘、电饭煲控制面板多种领域的面板、标志等外观件上,集装饰性与功能性于一身,其产品已经进入千家万户。
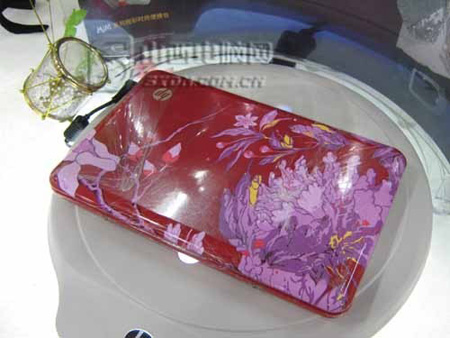
IMR产品图片(笔记本外壳)
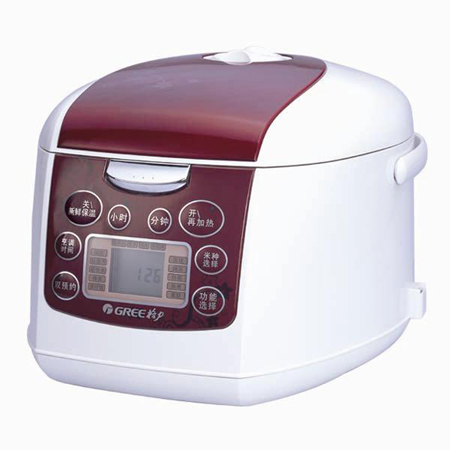
IMD产品(电饭煲)
通常的IMD工艺按照最终的产品表面是否有一层透明的保护薄膜,可以分为分为IML(IN-MOLD FILM/LABEL)、IMR(IN-MOLD ROLE)。
IML的中文名称是模内镶件注塑。其工艺非常显著的特点是:表面是一层硬化的透明薄膜(PC或者PET),中间是印刷图案层,背面是注塑的树脂层。油墨夹在薄膜和树脂中间,可使产品防止表面被刮花和耐磨擦,并可长期保持颜色的鲜明不易退色。
IMR的中文名称是模内转印(热转印或者热转写),此工艺是将图案印刷在薄膜上,通过送膜机将膜片与塑模型腔贴合进行注塑,注塑后有图案的油墨层与薄膜分离,油墨层留在塑件上而得到表面有装饰图案的塑件,在最终的产品表面是没有一层透明的保护膜,膜片只是生产过程中的一个载体。但IMR的优势在于生产时的自动化程度高和大批量生产的成本较低。IMR的缺点:印刷图案层在产品的表面上,厚度只有几个微米,产品使用一段时间后很容易会将印刷图案层磨损掉,也易褪色,造成表面很不美观。另外新品开发周期长、开发费用高,图案颜色无法实现小批量灵活变化也是IMR工艺无法克服的弱点。
模内注塑工艺是一项新兴工艺,同时也是一项综合性很强的工艺,它牵扯到油墨、薄膜片材、注塑树脂、注塑模具等。在这几项中任何一项出现问题,都会影响最终的产品,并给厂家造成损失。以下就这几项进行逐一分析,希望给大家提供有用的帮助。
(1)片材
模内注塑目前使用的印刷片材主要是PET、PC材料,以及PMMA。其中使用最多的是PET材料,市场上的PET材料种类繁多,既有正规大厂出产,又有其他来源的。如果最初的印刷材料没有进行一些必要的测试后,就会导致薄膜材料和油墨之间没有附着力,导致后面一系列的工艺徒劳无功。建议模内注塑的客户在使用不同批号的材料做注塑后,首先对材料的进行一些测试:
比如:利用油墨的附着力测试,来测试油墨是否在此材料上有附着。材料的耐温性测试,测试后期注塑时,材料是否可以承受注塑模具中的温度。
其实在进行油墨附着力测试最好的办法就是直接用UV油墨来测试,目前业界一般的UV油墨都必须在经过易附着处理的材料上印刷才会有附着力,如果UV油墨在此材料上有附着力的话,溶剂型油墨在材料上印刷肯定不会有问题。
(2)油墨
目前市场的注塑油墨以日系(十条、帝国、精工)和德系(宝龙)居多,国内有厂家在成产,但是在实际应用中较为少见,也较少有成功的案例。
油墨在使用过程中,一般需要注意如下问题:
a.油墨在薄膜材料上没有附着力
同油墨厂家确认油墨的使用范围使用条件,是否需要添加固化剂,是否需要专用稀释剂;同薄膜厂家确认薄膜的种类,以及是否经过一些易附着处理;
b.油墨印刷过程中会凝固、不下网。
一般的油墨添加固化剂后,油墨的使用时间会有所限制,有的油墨在添加两种固化剂以后,使用时间会变的更短,因此在印刷之前需要向厂家确认清楚;如果是单组份油墨只需添加稀释剂即可。
c.油墨在注塑时,出现“冲花”现象。
原因分析:油墨不耐高温所致或者油墨直接接触到了高温注塑树脂。
模内注塑工艺中,一般都在薄膜印刷的最后印刷一层溶剂型胶水,胶水一般起两方面的作用:黏着作用,使薄膜和注塑的树脂更加好的黏合在一起;保护油墨层,注塑过程中,高温树脂首先会融化已经完全干燥的胶水,在融化胶水的过程中,树脂的热量被部分吸收,进而减少油墨因为高温树脂所致的变色现象。
所以最后一层的胶水印刷,一般推荐低目数印刷(250目左右),一到两遍,保证胶水尽可能的厚。
同时油墨的皮膜干燥时间适当延长,温度适当提高,或者增加固化剂的添加比例,以此来提高油墨皮膜的硬度也会可以保证油墨具有较好耐冲性。
其他原因在模具部分中阐述。
d 注塑产品,树脂部分和薄膜分离
油墨是否完干燥完全,油墨中会有稀释剂、印刷过程中要添加稀释剂,在印刷最后稀释剂如果没有完全挥发就去注塑的话,会在注塑中继续挥发,由于此时树脂和确认黏合剂是否和注塑的树脂相配套。
电子标签印刷
所谓电子标签,就是指印刷后用在电子产品上的标签。如笔记本上的“windows”标示标签、生产厂家标签以及笔记本电池上面的标签。
电子标签使用的材料一般以PET、PC材料和合成纸为主,以及在PET材料上作出各种效果拉丝效果,磨砂效果等等。应用在电子标签上的油墨国内国外的厂商都有,价格和质量也是相差很多。
电子标签印刷的油墨在使用的过程中主要存在以下问题:
a.油墨在印刷材料上附着不好。解决方式:确认油墨和材料是否匹配;确认油墨是否干燥,一般的丝印油墨因为印刷的墨膜比较厚,所以需要采取强制干燥的方式来加快油墨的附着。如果是自然干燥,时间要保证充分;添加必要的固化剂。
b.印刷后的墨膜出现墨斑等现象。
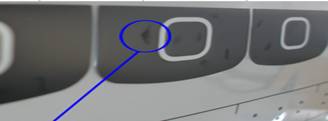
印刷墨斑
解决方式:确认使用的稀释剂是否和油墨相配套,稀释剂是否可以充分溶解油墨;确认油墨在使用时是否充分搅拌,一般来说油墨在新开罐时,其树脂颜料会沉淀在罐子的底部,这时需要充分搅拌一段时间去除墨样,加入稀释剂,加入稀释剂后仍需进行充分搅拌,保证油墨里面的树脂、颜料与稀释剂充分混合。印刷过程中,由于稀释剂的挥发,必要时在网版上酌情添加稀释剂,并搅拌;重叠印刷时,确认保证首印刷面的整洁,不要落下灰尘,避免水渍、汗渍;添加固化剂的油墨要保证固化剂和油墨、稀释剂均匀混合;确认胶刮的刀口部分是否有缺陷,是否需要更换新的胶刮。
c.油墨的黏度值较大,无法印刷。
解决方式:添加必要的稀释剂,UV油墨需要专门配套的稀释剂;油墨充分搅拌或者边加热边搅拌,特别适用于UV油墨,冬天温度低,油墨的黏度值大,如果依靠添加稀释剂会影响UV油墨的固化。
d.油墨的黏度值较小,像水一样在流淌,无法印刷。
解决方式是:建议添加适量的粉类物质,如消光粉(光泽型油墨不推荐),添加量一般在3%以内;同样可以把油墨放置在温度较低的环境(如冰箱)一段时间。
e.油墨出现气泡的原因及解决方法
出现气泡的原因有下面两种情况:含硅的油墨与非含硅油墨在一起使用时出现气泡;温度的变化导致油墨黏度的变化也会出现气泡,黏度大气泡容易出现。
解决方法:同油墨厂家确认使用的油墨的类型,比如调色时同是印刷在PET上的两系列的油墨,是否可以混用。在同一系列的油墨调色时,确认清漆和有色墨是否可以混用;添加消泡剂,并同油墨厂家确认此消泡剂的适用范围(适用于含硅油墨还是不含硅油墨);添加稀释剂,油墨充分搅拌后,要稍微静置一段时间。
f.印刷的皮膜表面出现针孔
针孔的外观首先是气泡,在干燥的过程中气泡破裂,周围的油墨没有及时流平,便已经干燥,这时出现针孔。印刷车间不洁净,存在灰尘、印刷材料表面有油污等原因都会造成针孔现象的出现。一般来讲,针孔现象是不可避免的,某些数目的针孔也是在可允许范围之内的。但是采取以下措施可减少针孔的出现:
重复印刷,印刷两遍以上;降低印刷目数,比如300目减为250目;使用无尘车间,减少灰尘;使用慢干性稀释剂,减慢稀释剂的挥发速率;增加胶刮的压力,放慢印刷速度。
g.印刷细小的文字、网点图像时,文字和网点丢失。
在印刷过程中,由于油墨干燥太快,导致细小文字和网点无法顺利的从网版转印到承印物上。
解决方式:使用UV油墨来印刷。UV油墨由于不含有挥发性溶剂,在细小文字和网点印刷时有较好的再现;换用慢干型的油墨或者油墨中添加慢干稀释剂,延缓油墨的干燥。
日化标签印刷
日化用品主要是PP、PE材料。这一类材料由于表面张力值较低,需要采取一些措施增加其表面的的张力值,来增加油墨的附着力。常用的增加表面张力的方法有:化学处理,火焰处理,电晕处理等。
值得注意的是,经过火焰处理后的塑料表面的效果有时效性,会在一定的时间之后消失,需要及时印刷,笔者所见过的最有成效的印刷方式就是火焰处理和印刷联动操作,火焰处理一般使用的是天然气。
有些客户在使用UV油墨印刷PP、PE材料时,经常出现印刷后的图案或者文字经过UV固化后缩小的现象。原因主要是UV油墨的黏度值太低,可以改用高粘度的UV油墨。
化妆品包装经常使用一些玻璃的标签材料,在此类材料上印刷时一般以强制干燥的油墨为主。干燥的温度和时间一般在100~130℃,30~50min为宜。
由于此类油墨一般为双组份油墨,在使用此类油墨时一定要注意选择合适的油墨稀释剂,确保稀释剂、油墨、固化剂三者之间良好的互溶。
特殊类的油墨的印刷
1.印刷线路板时使用的导电碳浆、绝缘油墨、导电银浆。
首先这一类使用的印刷材料一般是未经处理的PET材料,使用的导电碳浆一般以溶剂型为主,绝缘油墨常以UV型为主,银浆以溶剂型为主。
使用此类油墨时,需要注意如下问题:
a.先期的测试实验是必不可少的,测试油墨的附着力,测试油墨电阻值、耐电压、电阻率等等。
b.同时印刷时最好要在无尘环境中操作,防止灰尘落在本来就非常细小的印刷线上。
2在丝网印刷中,目前使用的银墨中镜面银较多。关于此类油墨的印刷需要注意以下事项:
a.银墨印刷时,因为其中银粉的粒径不同,需要采用不同的网目来印刷。对于粒径较大的网目一般在200目左右,才能保证银墨中银粉能够通畅的被印刷在承印物上。否则如果使用较高网目的话,在印刷初始是可以的,但随着印刷的进行,银粉中粒径较小的颗粒被转移到承印物上,较大的颗粒则留在网版,容易造成网目的被堵,无法继续印刷。
b.镜面油墨由于本身黏度值较小,像“水”一样。在印刷时,必须快速印刷,防止油墨在网版的流淌、渗透污染到承印物,同时镜面油墨的干燥最好在冷风下干燥,这样获得的镜面效果最好。
镜面油墨里面的金属成分较多,印刷时一般不耐折,不耐划伤,印刷时需要注意尽量不要把镜面油墨印刷在模切的位置,避开模切工具的冲击。印刷完镜面油墨后,在其背面要有打底的油墨来保护镜面层,并需确认镜面油墨和起保护作用的油墨是否会反映影响镜面油墨的镜面效果。
丝印油墨的调色
在丝网印刷工艺中,需要调制的油墨也较多。由于丝印油墨调制墨没有同一的标准可参照,不同的油墨厂家里面的颜料体系不一样,实际生产不同的工艺都会影响丝网油墨调的颜色。下面就丝网印刷油墨的调色谈一下自己的体会。
1、调色前的准备工作:
首先调色以前需要和客户确认如下事项:印刷材料是何种种类?印刷材料有无底色?印刷材料的哪一面需要印刷?调色墨需要印刷几遍?印刷的网目数?印刷完调色墨以后是否需要打底色,印刷打底色需要的网目数?
2、丝网印刷调色的工作有时不是一次调色就能让客户满意的,如果客户认为调出的颜色有偏差,需要注意以下问题:
首先调色时,客户经常会提供潘通色号作为标准,但是由于潘通色卡只是胶印使用的色卡,且胶印和丝网印刷存在较多的差异,所以调色只能做到颜色接近。其次同一家的油墨还原同一家的调色墨基本没有问题。最后用一家的油墨来还原其他家的油墨,由于油墨配方的问题,也是只能做到大致接近。
同时在调色时,调色师傅通常会将自己调的颜色先行印刷一下测试印刷效果,如果调色师傅的印刷效果客户认可,客户自己印刷时却没有印刷出这种效果的话,一般应从客户打样时的印刷目数高低、印刷压力大小、网版乳胶厚薄、刮刀硬度及印刷速度来综合考虑分析。
【点击查看更多精彩内容】
相关新闻:
涨价狂潮下油墨等原材料的价格将走向何方
油墨使用知识十问十答
2011年印刷产业发展:油墨等原材料价格走向何方
油墨出现粉化现象的原因及解决方法
- 关于我们|联系方式|诚聘英才|帮助中心|意见反馈|版权声明|媒体秀|渠道代理
- 沪ICP备18018458号-3法律支持:上海市富兰德林律师事务所
- Copyright © 2019上海印搜文化传媒股份有限公司 电话:18816622098